The story of Braheborg
A great lake without a shipyard. And a dire need of a new double ended ferry. This is the story of how the ferry Braheborg came into existence through the magic of project management.
At a quick glance:
- The lack of a large shipyard in lake Vättern made it impossible to build on site.
- Project made possible through an intricate production plan, construction off site, vast project management and special transports.
- Open dialogue and handling of a requested construction change mid build.
-
Relocated staff from Finland to Sweden for a whole year.
-
Results: A ferry capable of handling rough weather with more stability than its predecessor, and a happy customer.
In the early 2010s, the Swedish Transport Administration was in need of a new, larger ferry to replace an old one in Swedens second largest lake Vättern. They therefore conducted a procurement. There were two catches, though:
Firstly, there aren’t any shipyards in lake Vättern that can be used to build a large ferry, and to construct a temporary shipyard would be very expensive. The only possible building site was a dry dock, that was lacking the necessary infrastructure to build a boat.
Secondly, the Swedish Transport Administration wanted a ferry with a width of 14 meters – which incidentally also is the maximum width of the Göta canal, the only waterway from the ocean to Vättern. The maximum permitted width of a boat in the canal is seven meters. That rendered this passageway impossible to use.
So there really only was one solution for Työvene, who won the procurement: Production offsite, a vast amount of project management and relocation of staff from Finland to Sweden.
Intricate production plan
In order to build the ferry, which was to be named Braheborg, Työvene made an intricate production plan. The ferry was built part by part in Työvenes shipyard in the city of Uusikaupunki, Finland, and in a partner shipyard in Latvia. From there, the part blocks where hauled by sea to the Swedish city Västervik. There, they were loaded onto trucks and transported to Huskvarna, a part of the city Jönköping that lies on the shore of lake Vättern.
We had to plan several special arrangements for the transport to Huskvarna. For example, just next to the dry dock there were bridges that was too low for our transports, so we had to use mobile cranes to lift the blocks over the bridges.
Janne Kosomaa, main project manager at Työvene for the build of Braheborg.
Foto: Työvene
Fortunately, the Swedish Transport Administration have a dry dock for ferry maintenance in Huskvarna, which the administration made available to Työvene during the build of Braheborg.
In the dock, the blocks were assembled, painted, isolated and thereafter outfitted with all the onboard equipment, the interior and the machinery.
Happy customer
With all the blocks fitted, the results was a ferry with a capacity of 34 cars and 397 passengers – the largest ferry ever to traffic the route between the city Gränna and lake Vätterns largest island Visingsö. At the Swedish Transport Administration, they are happy with the results of Työvenes way of working and managing projects.
Työvene did a good job. It was complicated given that the ferry was assembled in Huskvarna and not in their own shipyard. The construction progressed as planned and the results were good.
Fredrik Skeppstedt, project manager at the Swedish Transport Administration.
Fredrik Skeppstedt was responsible for the documentation during the Braheborg procurement, and also had the role of inspector at the shipyards and in the dry dock in Huskvarna.
Relocated staff
To be able to handle all the necessary project management, Janne Kosomaa and five of his colleagues moved to Huskvarna, where they lived for about a year. There this project organisation worked next to the dock, in construction sheds Työvene rented to use as offices, changing rooms and workshops.
– This was a very special project, a once in a lifetime experience. But we will absolutely do it again if needed.
During that year, Janne Kosomaa and his colleagues on site periodically were accompanied by between 10 to 60 craftsmen, depending on the scope and the complexity of the task that were at hand at the time being.
– The craftsmen came to perform a specific task, and then they went back home again. To have this kind of flexibility is the Työvene way. It allows us to be cost efficient, while it also enables us to fulfill the needs of the customer.
Change order during the construction
During the construction of the ferry, the Swedish Transport Administration realised that it was necessary to make changes to the ferry’s blueprints, as they understood that the crew needed another break room, in addition to the wheelhouse.
– If the customer wants something, then we really strive to fulfill their requirements. That is one of our philosophies. Therefore, we changed the design in the middle of the build, said Janne Kosomaa.
By redesigning some of the passenger compartment, Työvene were able to add a room with a small kitchen for the crew.
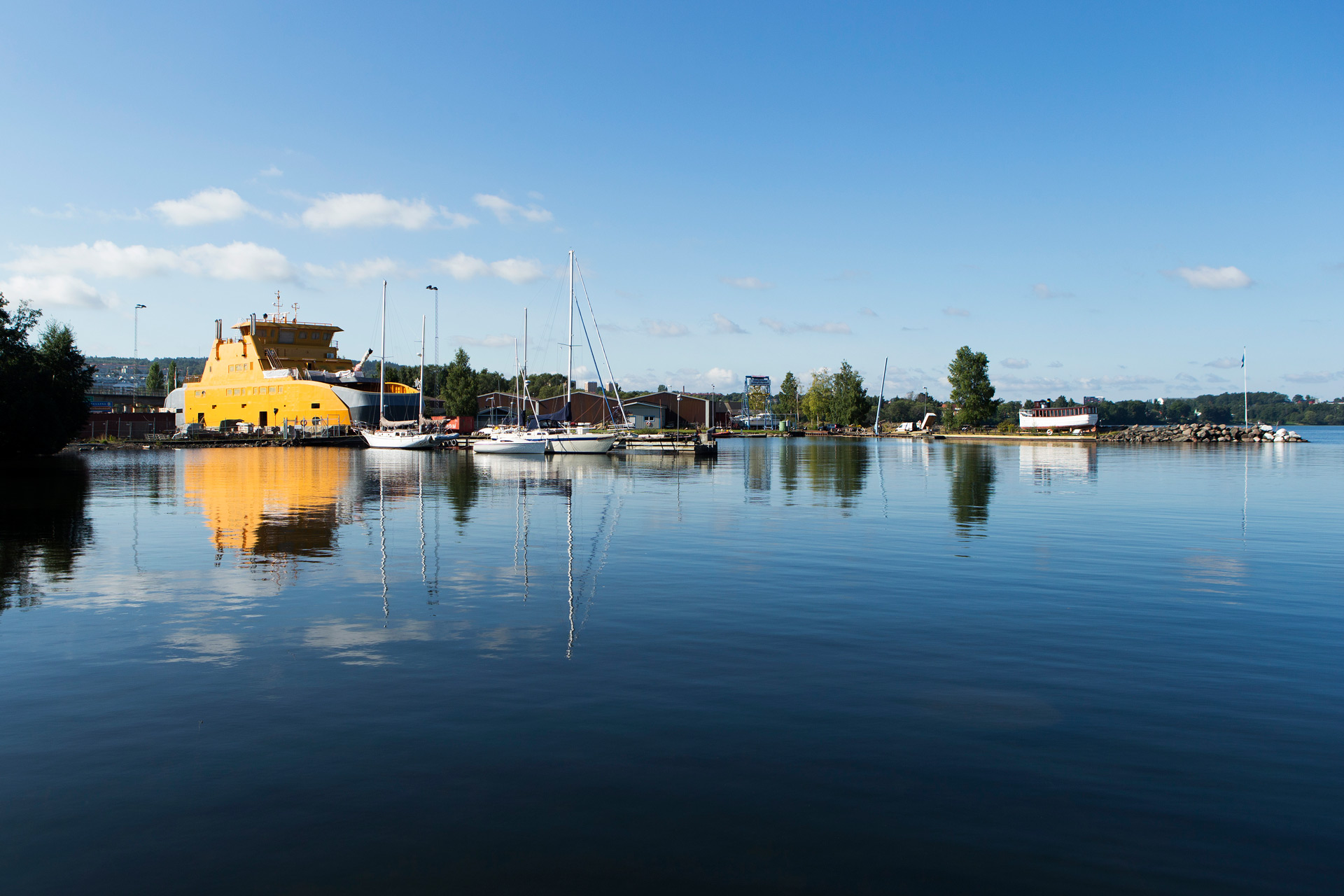
The double ended ferry Braheborg has the capacity to transport 34 cars and 397 passengers on the route Gränna–Visingsö. The ferry will never leave lake Vättern, as it is too big for Göta canal, the waterway from the lake to the sea.
Foto: Kasper Dudzik
The results
The first parts were delivered to Huskvarna by the end of October in 2012. 1,5 years later – in January 2014 – the double ended ferry Braheborg was delivered to the Swedish Transport Administration. Today, Braheborg operates on a daily basis alongside the ferry Ebba Brahe, connecting the city Gränna with lake Vätterns largest island Visingsö. Sometimes, during scheduled maintenance, they are assisted by Christina Brahe, the predecessor of Ebba Brahe that was built in the 1970s.
The Braheborg crew appreciates the ferry’s design as it’s a substantial update.
Braheborg is more stable in bad weather. It’s a big difference compared to the old ferry.
– Braheborg is more stable in bad weather. It’s a big difference compared to the old ferry. It is also equipped with a bow visor which minimizes the amount of water splashing up onto the car deck. It does make a difference on the ferry route, said Fredrik Skeppstedt.
The order
The Swedish Transport Administration procured a turnkey product, based upon pre-determined functional requirements and a concept design that was included in the tender. Työvene designed and built the ferry Braheborg based upon the requirements, for example:
- A double ended ferry with extra space for passengers.
- A capacity of 34 cars and 397 passengers.
- A draft of 3 metres and a speed of 13 knots.
- Bow visor for protection in bad weather.
- Built for service area D, that has higher requirements than service area E, which in turn effects the design and equipment.
- A length of 58,3 metres and width of 14 metres – the dimensions were limited by the size of the dry dock.
- Classification made by Bureau Veritas.
- Production closely supervised and inspected by the Swedish Transport Agency.
More customer cases
Ursa – Työvene’s first ever dredger
The dredger Ursa will be used to maintain the depth in the Vistula Lagoon Canal and fairway that connects the Polish city of Elbląg with the Baltic Sea.
Västtrafik’s ferries over Göta River
Read the story about how Swedish Västtrafik AB managed to solve commuter needs with sustainable ferries.